Cathodic Protection
Cathodic protection is an electrochemical process that halts the natural corrosion of metals in a particular environment, such as water.
About Corrosion
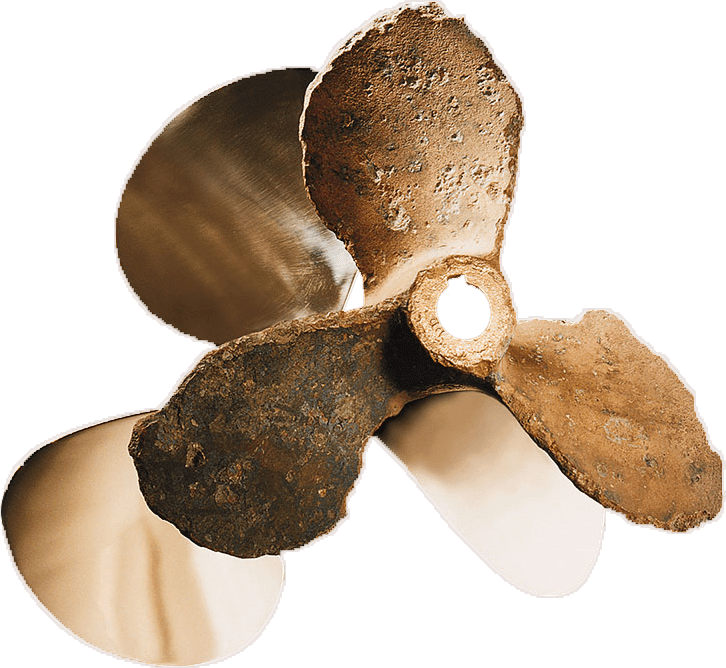
Corrosion takes place in all types of water and the impact on boats and coastal structures can be catastrophic. MGDUFF marine cathodic protection systems help prevent this kind of damage, protecting boats and structures and the investment in them.
All commercial and leisure vessels and onshore structures are vulnerable to corrosion. How does corrosion happen? In layman’s terms, a metal will corrode as a result of a chemical reaction to its surroundings, such as water.
Corrosion takes place in all types of water – fresh, salt and brackish – and as a result of an increase in the number of tidal barriers and enclosed marinas, boats of every kind are now regularly moving between all three. It is vital that the right anodes are used for each type of water.
This is why cathodic protection products from MGDUFF are so important. Our high-quality anodes, manufactured to strict quality and environmental standards, offer enhanced protection against catastrophic damage and costly repair bills.
All commercial and leisure vessels and onshore structures are vulnerable to corrosion. How does corrosion happen? In layman’s terms, a metal will corrode as a result of a chemical reaction to its surroundings, such as water.
Corrosion takes place in all types of water – fresh, salt and brackish – and as a result of an increase in the number of tidal barriers and enclosed marinas, boats of every kind are now regularly moving between all three. It is vital that the right anodes are used for each type of water.
This is why cathodic protection products from MGDUFF are so important. Our high-quality anodes, manufactured to strict quality and environmental standards, offer enhanced protection against catastrophic damage and costly repair bills.
Galvanic corrosion
Galvanic corrosion is the principal type of corrosion from which boats and onshore structures are at risk. This type of corrosion is caused by the connection of dissimilar metals to each other while in water.
If these metals are immersed in water and are in direct electrical contact, they form a simple battery. The battery produces a small voltage, driving a current from one metal component to the other through their metallic connection, causing one of the components to corrode.
Which component corrodes depends on the position of the two metals in the galvanic series. The metals at the top of the series act as an anode and corrode, while those lower down this ranking system are protected from corrosion (and are labelled more noble metals).
If these metals are immersed in water and are in direct electrical contact, they form a simple battery. The battery produces a small voltage, driving a current from one metal component to the other through their metallic connection, causing one of the components to corrode.
Which component corrodes depends on the position of the two metals in the galvanic series. The metals at the top of the series act as an anode and corrode, while those lower down this ranking system are protected from corrosion (and are labelled more noble metals).
Electrolytic corrosion
Electrolytic corrosion is caused by stray current leakage. Stray current leakage occurs when a fault on board a boat causes an electric current from an external power source, for example a battery or onshore power supply, to pass out through the hull or a fitting in the hull, and flow through the water. Where this current exists, corrosion will take place, often with dramatic results.
How to spot corrosion
Corrosion to steel and aluminium boats takes two forms: localised pitting to areas such as the hull plate, rudder and bilge keel; and general wastage of the hull plate, which often occurs below the paint coating.
The impact of this corrosion can be disastrous and very expensive. Localised pitting can lead to the complete penetration of the hull below the waterline, and general wastage can critically weaken the hull.
Corrosion to wooden and GRP boats takes place mainly to the stern gear, such as the propellers, shafts, shaft brackets, stern tubes and rudders, which are critical to the viability of the craft and expensive to replace. This type of corrosion can take various forms, from localised pitting to components, such as the propeller and shafts, to the decomposition of the propeller alloy. The failure of something as small and inexpensive as a split pin can lead to the loss of a propeller.
The impact of this corrosion can be disastrous and very expensive. Localised pitting can lead to the complete penetration of the hull below the waterline, and general wastage can critically weaken the hull.
Corrosion to wooden and GRP boats takes place mainly to the stern gear, such as the propellers, shafts, shaft brackets, stern tubes and rudders, which are critical to the viability of the craft and expensive to replace. This type of corrosion can take various forms, from localised pitting to components, such as the propeller and shafts, to the decomposition of the propeller alloy. The failure of something as small and inexpensive as a split pin can lead to the loss of a propeller.
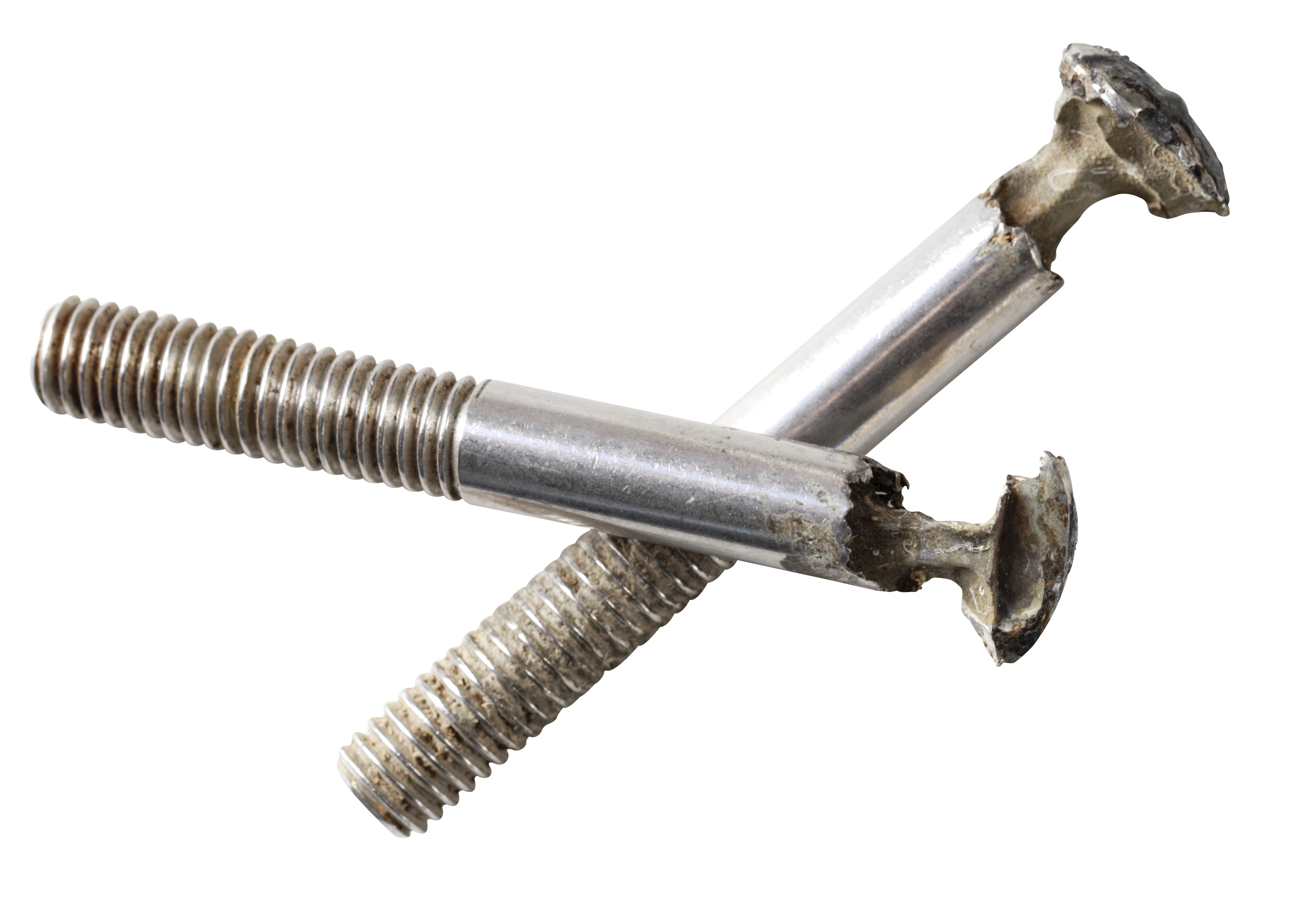
How to Prevent Corrosion
Selecting the right materials
Selecting compatible materials during the construction of a boat can help prevent corrosion. When this is not possible, the metals chosen should be isolated from each other. Similarly, when maintenance is carried out, the same principals should be strictly applied. In particular, it should be ensured that the fastening and pins used are of a compatible material and of the highest quality.
Painting your boat
Applying the correct painting system to a boat will help protect it from corrosion. Advice on the most appropriate coating system to use should be sought from your paint supplier.
We recommend the application of an anti-corrosive primer if anti-fouling is to be used. If a copper anti-fouling is being used, paint must not be applied directly to bare metal surfaces
Electrical installation
The proper installation of electrical components will reduce the chance of stray current leakage and electrolytic corrosion. The easiest way to avoid electrical problems is to have electrical work carried out by a qualified marine electrician. However, if you are doing any work, we recommend the following:
- Use only high-grade insulated wiring of suitable capacity. Undersized wiring will cause resistance and voltage drop.
- Clip or support all wires at suitable intervals to prevent fatigue and fracture.
- Use only corrosion-resistant terminals and connectors, and ensure they are clean and tight.
- Attach only the main battery lead to the battery terminals.
- Fit an isolation switch in the battery circuit.
- Ensure that all battery circuits are correctly fused.
- Keep all wiring, connections and junction boxes above the bilge area and other areas likely to become wet.
Maintenance
Regular maintenance will help prevent corrosion. Metal work, paint work and electrical components should all be regularly inspected.
With regard to steel boats, it is vital that special attention is paid to areas around the water line. These are particularly vulnerable but receive no protection from anodes above the water line.
With regard to steel boats, it is vital that special attention is paid to areas around the water line. These are particularly vulnerable but receive no protection from anodes above the water line.
What is Cathodic Protection?
Cathodic protection is an electrochemical process that halts the natural corrosion of metals in a particular environment, such as water.
In scientific terms, it works by superimposing an electrochemical cell more powerful than the corrosion cell. Put more simply, it diverts the corrosive process away from the metal components of a boat or structure and onto the anodes. These anodes are attached to the metal components of a boat or structure and, because they are made of a metal higher placed in the galvanic series, they attract corrosion and protect against damage. The anodes corrode instead of the boat or structure.
The number and size of anodes that should be used depends on what a boat or structure is made from and the size of the surface being protected. Also, the size of a boat or structure, the type of water it is used in and the length of time it spends in the water have a bearing on how often the anodes should be replaced.
In scientific terms, it works by superimposing an electrochemical cell more powerful than the corrosion cell. Put more simply, it diverts the corrosive process away from the metal components of a boat or structure and onto the anodes. These anodes are attached to the metal components of a boat or structure and, because they are made of a metal higher placed in the galvanic series, they attract corrosion and protect against damage. The anodes corrode instead of the boat or structure.
The number and size of anodes that should be used depends on what a boat or structure is made from and the size of the surface being protected. Also, the size of a boat or structure, the type of water it is used in and the length of time it spends in the water have a bearing on how often the anodes should be replaced.
If you are unsure, you can always use our Find My Anode tool to help you find the anode for your vessel.
We recommend boats that move into fresh water from salt water or vice versa for more than two weeks should have their anodes changed
Related